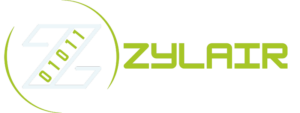
Automating Risk Reduction
Imagine a job where the mundane, repetitive paperwork is reduced, and stats just…appear!
Imagine a job where the mundane, repetitive paperwork is reduced, and stats just…appear!
Early in my manufacturing career, I always assumed that manually logging an incident report was just part of the job. Writing down the details, photocopying forms, chasing signatures, and filing paperwork into a dusty folder was standard procedure. One slow afternoon, I did the maths — out of curiosity more than anything else.
It turns out our Health and Safety team were spending around 15 minutes per incident, per person, just to fill out paperwork. At first glance, that might seem harmless enough. But stop and consider the cumulative impact—over a week, a month, and then a year. In one facility alone, I calculated that we were losing over a hundred working hours annually, dedicated to archaic manual logging.
The numbers stopped me in my tracks, and if you’re honest, you might be experiencing something similar at your workplace. Health and Safety professionals rarely take note of time consumed by routine administrative tasks. We’re usually more focused on prevention and immediate concerns—yet we unwittingly drain valuable time into manual logs, spreadsheets, and scans. It’s a subtle but substantial leak in our daily productivity.
As a manager, I had always accepted the time spent manually filling forms was a necessary evil—a minor, unavoidable inconvenience. But my real wake-up call came from reviewing not just the wasted hours, but the broader impacts behind our manual reporting.
First, it puts an undeniable human burden on my Health and Safety team members. Whenever I spoke to colleagues about paperwork, their reactions were a mix of irritation, resignation, and hidden frustration. After an incident, they wanted to be in the factory floor ensuring worker safety or working on preventive measures—not chained to desks recording trivial data. Over time, this monotony breeds dissatisfaction, diminishes motivation and may subtly affect retention.
From a financial standpoint, the impact isn’t minimal either. Those hours spent logging manually might seem insignificant, but add them together and they become a significant cost. Add to this the possibility of inaccuracies—manual entries inevitably lead to errors—causing delays and potential incident misrepresentations leading to further compliance risks. Manual systems also make crucial trends and insights harder to spot. The reactive cost to these hidden inefficiencies—legal requirements, accident compensation, lost production—far outweighs the initial obvious concern.
Operationally, I learned that our reliance on dated manual logging results in slower reaction times. Any delay hinders our ability to analyse incidents effectively and stifles our continuous improvement efforts. Over time, your team might unknowingly start to see incidents as cumbersome annoyances rather than valuable learning opportunities.
Realising the scale of the problem compelled us to rethink our approach. ‘Digital safety systems’ were becoming prevalent—but honestly, I initially saw them as complex, expensive solutions more suited to large corporations than my factory floor. Still, we couldn’t ignore the issue much longer, and our frustration reached its tipping point. As we experimented with available solutions, I found that modern ‘incident reporting tools’ could be simple, intuitive, and user-friendly—something my initial scepticism had prevented me from exploring earlier.
We moved away from pen-and-paper records to a simple mobile-based app that allowed instant input, real-time notification to relevant personnel, automatic data entry, and secure cloud storage. Teams could quickly photograph, dictate, or tap-and-select incident details into their devices on the factory floor—immediately returning to critical tasks. No more paperwork headaches, no more desks cluttered with paperwork, and no chasing for signatures or misplaced documents.
It wasn’t revolutionary—we didn’t invent anything new—but shifting to ‘safety report automation’ quickly became one of the simplest and most impactful improvements I’ve implemented. The system collates data automatically and proactively helps identify incident trends or risky working areas, giving our Health and Safety professionals immediate insights that pencil and paper could never deliver.
I initially moved towards automating incident reporting merely expecting to reclaim those fifteen wasted minutes per log. Yet we gained far more valuable returns than we expected. Our team members received immediate relief from monotonous tasks, experienced improved morale, and dedicated their skills to proactive safety monitoring and prevention strategies.
Financially, we’ve erased the hidden cost of overlooked mistakes and overstaffing administrative roles. Errors are dramatically reduced, risks appropriately mitigated, and repair or downtime costs minimised through enhanced proactive management. Digitising has also improved compliance and transparency, simplifying audits and regulatory inspections.
Operationally, as a manager, I have gained unprecedented real-time insight into incidents, trends, and proactive safety opportunities—something that paperwork could never provide. Digital systems support faster and smarter decision-making, allowing my team to focus on learning and forward-thinking solutions. They’re less likely to view incidents simply as burdensome paperwork, and more likely to embrace them as opportunities for positive learning and growth. Admittedly, it’s taken time and reflection to fully appreciate all these unforeseen benefits.
If you’re still logging your incidents manually, the truth might gently sting—but you’re wasting valuable time and effort too. Removing the burden of manual incident recording is no longer luxury—it’s a smart and necessary progression that directly enhances safety culture, operational effectiveness, and employee satisfaction.
Let me share from honest experience: moving beyond manual logs isn’t complex, disruptive, or unmanageable. With powerful digital tools at our fingertips, it simply makes sense. It was a lesson I learned late, but one worth sharing now: embracing safety report automation empowers your workforce, elevates your outcomes, and deeply enriches your entire health and safety approach.
I remember the moment clearly. It was a Tuesday morning, bustling with the usual hum of machines and activity, when I noticed our shift supervisor deeply agitated, holding his clipboard full of paper report forms. Amongst these stacks of unchecked, forgotten paperwork was buried something important—a series of near-miss reports from the night shifts, clearly flagged but overlooked due to sheer volume and monotony of paperwork. Later that morning, what began as a near miss evolved into a significant machine breakdown, halting operations for hours.
The issue wasn’t negligence; our team was dedicated to safety and committed to following our established processes. The real cause? The reporting was cumbersome, dull, and time-consuming to review. It meant genuinely important incidents were hidden under piles of routine paperwork, practically begging to be ignored or overlooked. A flood of complicated forms created a burden rather than promoting active safety engagement, leading essential signals to be lost in the bureaucratic noise.
Make no mistake, the cost of these overlooked near-misses can quickly add up, beyond what you’d initially think. I learned this the hard way. Take the operational hit: machinery downtime meant temporary stoppages and production delays, sending ripples of disruption throughout our supply chain and adversely impacting our delivery schedules and reputation with valued clients.
Then came the financial repercussions. Emergency repairs, overtime payments, production delays—all unexpected expenditures due to something that could’ve been proactively addressed much earlier. It’s shockingly easy to underestimate these hidden costs until they demand immediate, reactive attention—and by then it’s usually costly damage control rather than preventive maintenance.
However, nowhere was the blow felt as deeply as in human factors. Trust eroded, morale took a hit, and our safety culture suffered. Employees wondered, “why bother filling reports no one reads?” Seeing their valuable insights vanish into paperwork black holes was both demoralising and frustrating. It undermined their motivation and commitment, something I deeply regretted.
Facing these consequences taught me a valuable lesson: health and safety professionals don’t need to be trapped by outdated processes. I knew there had to be a better way—something straightforward, intuitive, and digital that could slot neatly into our existing workflow without upending everything. We explored options, piloted some programmes, and soon settled on a practical solution: intuitive safety compliance software designed specifically for manufacturing environments.
This digital safety system allowed near misses and incident reports to be logged easily, intelligently categorised, and—most importantly—flagged in real-time. Instead of filtering through countless stacks of paperwork, our teams gained immediate visibility to urgent safety alerts and could act proactively and decisively. Equally crucial, these tools slotted effortlessly into our staff’s daily rhythms, easily accessible via mobile or tablet devices directly on the shop floor, making the transition seamless—and relief immediate.
The beauty of safety automation isn’t about fancy software or overly complex dashboards. It’s about using smart technology that simplifies safety management rather than complicating it. More than anything, implementing digital safety systems was about empowering people. It freed our managers from paperwork, allowing more time for active, on-the-floor presence, building relationships and proactively coaching teams on safety.
Shifting towards health and safety automation for reporting transformed our entire team’s safety attitude and participation. For the first time, we had transparency and immediate visibility, allowing quick reactions that helped prevent bigger incidents. Seeing reports automatically escalate and being acknowledged encouraged our staff to continue engaging proactively—a positive feedback loop we had never seen before.
Because adopting these digital tools meant we no longer wasted time manually processing and deciphering paper reports, our team’s approach transformed from reactive to genuinely proactive. Compliance became a continuous daily habit rather than forced activities at month’s end. In other words, we finally developed a living safety culture powered by action—not merely paperwork.
As a result, safety compliance improved, people felt genuinely heard, and morale significantly strengthened. Mistakes are inevitable, yes, but the vital difference became how we responded—swiftly, openly, calmly. We hinged upon collaboration rather than simply assigning blame or becoming trapped in endless admin work.
If, like me, your desk (and brain) have ever felt weighed down with endless files of ignored or barely-read reports, consider adopting safety compliance software. Digital safety systems bring reporting alive, activate positive team engagement, and prove that reports can—and should—be tools of active improvement instead of simply formalities that no one reads.
When was the last time you read through one of your Environment, Health and Safety (EHS) reports and honestly felt it captured the reality of your shop floor? Let’s face it—we’ve all looked at a safety report once or twice and wondered if it was even talking about our workplace. If your reports feel detached from reality, maybe it’s time to challenge the sacred workflow of top-down safety reporting.
Early in my management career, I relied heavily on supervisors and experts away from daily operations to draft our safety documents and EHS reports. On the surface, it made sense. These folks were trained specifically to look for hazards, after all. But a blunt realisation woke me up one morning: The people directly managing risks on the floor—the operators, technicians, and line managers—had become merely passive recipients of a safety narrative they hadn’t shaped. And unsurprisingly, they felt disconnected from it.
This became evident to me one memorable day during an audit. When asked about clarity around a particular safety procedure from our latest reports, one of our operators honestly replied, “I couldn’t tell you—never read it. Probably written up in the offices, I reckon.” Fair enough—why would they engage deeply if the reports didn’t reflect their experiences? That simple moment was a wake-up call: Without employee engagement, your safety practices might as well live in dreamland.
The conventional workflow for creating EHS reports typically follows a predictable path: senior management and safety specialists assess risks, outline guidance, then delegate actions down the ladder. Operational teams and shop-floor staff are left to implement the changes without being sufficiently involved in creating the safety narrative they’re expected to embody.
I’ve been there myself, guided initially by a mistaken belief that too many inputs would slow things down or muddy the clarity of reporting. But here’s the hard truth I learned the tough way: Keeping frontline employees out of the reporting loop means ignoring essential, practical knowledge. Worse still, this exclusion breeds cynicism about safety reporting itself.
Let’s break down the damage. First, reports written primarily by off-floor teams tend to employ generic templates. These tick-box exercises might sound impressive in management audits, but they rarely highlight real practical issues or opportunities for improvement specific to your plant floor.
Secondly, this disconnect creates a silent risk—workers disengaged from safety procedures or reluctant to flag genuine issues because of doubt concerning action or follow-up. Put bluntly, ignoring on-floor insights doesn’t just cost efficiency—it can directly impact safety posture in a tangible and negative way.
So, real talk—how did we address this? Admitting the problem was the first step. Once we understood the disconnect, we started breaking down the old, bureaucratic boundaries. We restructured our EHS reporting process from the ground up, intentionally putting operators and frontline supervisors squarely at the heart of safety discussions and the authorship of reports.
Initially, it seemed risky to shift responsibility this way, sparking fears of inconsistencies, quality issues, or resistance. But what happened next surprised even me, a seasoned skeptic by nature.
Armed with user-friendly digital safety report automation tools, our shop floor workers began capturing details, observations, and near misses in real time, faster and more accurately than ever. No more writing scraps on crumpled paper. No more waiting until the end of shifts to recall issues, reducing valuable detail to vague bullet points. Digital EHS automation meant their inputs immediately became part of the shared conversation and shaped actions faster.
Slowly and mindfully, we built processes around their feedback rather than imposing top-down safety procedures onto them. We asked them openly, “What’s working, what’s not—and what do you think?”. And guess what? They told us explicitly. They shared details about machines needing better guarding, procedures that slowed them down, and even highlighted habit-formed workarounds no one had clocked before.
Instead of bureaucratic confusion, this mindset promoted clarity, ownership, and a genuine safety-first mentality. Workers weren’t passively receiving safety mandates—for the first time in a long while—they became architects building the safety culture themselves, sharing responsibility and pride in safety outcomes.
But talk alone isn’t proof—results matter. And I wouldn’t ask you to just trust me blindly on this. When we shifted responsibility for EHS reports closer to the operational teams, tangible benefits emerged quickly.
In terms of reporting speed alone, automated frontline reporting cut delays dramatically. Suddenly, insights that previously took days or even weeks to circulate could be available within minutes. Safety report automation tools integrated easily into our existing manufacturing software, meaning we could react faster, investigate better, and allocate resources more effectively.
Auditing days shifted from nerve-wracking to confidence-boosting events. Our team could clearly articulate procedures and hazards because they wrote them. Auditors regularly remarked on how grounded and practical our safety insights became—no vague platitudes; just spot-on guidance reflecting shop-floor realities.
And of course—most important—our safety metrics improved measurably. Lost-time incidents dropped because the reports now called out genuine frontline risks proactively, not reactively. Greater visibility of hazards led to quicker, smarter interventions. People took pride in fixing issues they personally had flagged because they felt true ownership.
The ripple effect of putting reporting power firmly in the hands of those closest to the hazards has been eye-opening, a real improvement in empowerment, communication, and most importantly, genuine safety improvements. It transformed our approach from a generic, compliance-driven EHS box-ticking exercise into a thriving workplace safety culture enriched by genuine care and practical knowledge.
So next time you’re glancing at a freshly printed EHS report, ask yourself honestly—is this a genuine voice of your frontline team? Perhaps it’s time to reconsider who’s holding the pen and drive safety from the floor up.
I used to think my safety protocols were airtight—manual forms filled out meticulously, spreadsheets updated regularly, binders full of health and safety procedures organised neatly on a shelf. On the surface, it looked perfectly tidy and efficient. But deep down, I noticed something quietly corrosive brewing in our daily routine. Those rigorous manual tasks were subtly becoming more of a hindrance than a help.
Let me share a thought that might make you pause, as it once made me: If your team finds your safety reporting system frustrating or unnecessarily complex, are you really safeguarding their wellbeing—or just ticking boxes? The truth hit me hard after years spent in manufacturing—safety procedures are only as effective as the team’s willingness to buy into them.
Some of the biggest risks lurking in your manufacturing processes could actually stem from your own safety practices. I discovered this in our own plant one month when reviewing near-miss reports. Shockingly, the majority of the incidents stemmed not from careless behaviour, but from frustrations bubbling from our cumbersome, manual reporting processes.
Here’s a scenario many of you might know too well: workers would face an issue on the shop floor—minor spills, equipment malfunctions, or minor finger injuries. Each incident required them to stop the task immediately, fill in paper forms by hand, and hunt for the supervisor to file the paperwork.
Because the paperwork process was tedious, some workers found that—for minor incidents—it was easier to skip reporting altogether. Others would leave it to the end of the shift, by which time details were foggy, accuracy compromised, and follow-ups far less effective. It was alarming, really—our very attempts to keep people safe were inadvertently discouraging incident reporting, ironically making our workplace potentially more dangerous.
I realised we were essentially punishing our staff for caring—burdening them with bureaucracy instead of empowering them to prevent hazards quickly and effectively. Manual data entry into spreadsheets increased error rates, slowed down communication and follow-ups, and made it harder for safety managers to spot trends or intervene proactively.
Something had to give. We needed a better approach—one that would speed up incident reporting and empower our team to readily share insights, not burden them with rules and outdated paperwork.
Initially, the idea of switching to an automated safety solution felt daunting at best and complicated at worst. Like many safety managers I’d met in my career, we struggled internally with concerns. Could our shop floor teams learn and use new software easily? Would automating mean reinventing every safety process we’d spent months perfecting? And, admittedly selfishly, would adopting a digital solution cost me valuable time and energy?
Despite initial reservations, we began small—no major overhauls, no convoluted layers of complexity. Just practical, easy-to-use digital safety systems that slotted naturally into our day-to-day activities.
Our first step was digitising incident reporting. We swapped pen-and-paper forms for simple incident reporting tools operable right from mobile devices already carried by supervisors and teams. From spotting a safety hazard to submitting reports and taking action—everything happened seamlessly within a few intuitive click-through screens. And importantly, the platform integrated with our existing scheduling and work-tracking tools effortlessly.
As we expanded our automations, we kept one clear rule at the forefront: any new safety enhancement had to plug directly into our existing workflow. Systems needed to be intuitive enough that no training session lasted more than ten minutes. After all, if adopting a tech solution became a job in itself, we’d simply be substituting old tedious manual systems with new convoluted digital ones.
Soon, teams across the floor found the new incident reporting and corrective action tracking simple and lightning-fast. Supervisors now had instant access to essential safety data exactly when they needed it—for example stepping onto the line or during safety briefings. Employee friction disappeared, and reporting surged almost overnight.
Perhaps you’re wondering, “So, did automating really make that much difference to compliance?” Absolutely—and then some. Our realisation was clear: keeping compliance strong means making it as effortless as humanly possible for front-line teams.
Because the digital incident reporting tools allowed us to connect data instantly—from reporting to corrective actions, from trends to solutions—our staff quickly saw practical outcomes to their proactive reporting efforts. Before automation, delays meant teams rarely saw rapid action or meaningful changes, leading to cynicism about the purpose of meticulous reporting procedures. Now, prompt follow-ups and immediate communication reinforce the value of reporting, encouraging teams to stay actively engaged.
Our safety culture evolved significantly. Workers now regularly suggest further digital safety system improvements themselves—proactively looking for streamlining opportunities and ways to simplify further. Today we receive more near-miss reports in one month than we used to receive in six, not because we’re seeing more unsafe incidents—but simply because our system no longer prevents people from sharing their insights.
In fact, the automation opened up entirely new ways of approaching our safety governance. Automated reminders helped us track training expirations effortlessly; sensor integrations meant audits happened in real-time, improving visibility significantly; QR codes around critical safety zones instantly delivered relevant protocols and updates right onto staff mobile screens.
Compliance became second nature, embedded into the culture itself—not because people were threatened with discipline or gently nudged to do the right thing, but simply because automation trimmed all the unnecessary complexity out of the process.
Looking back, if you’d told me two years ago that automating safety procedures could revitalise my team’s attitudes towards compliance, I’d have smiled politely and privately considered you a little optimistic. But here I stand, genuinely grateful that we questioned our comfortable but outdated methods.
The good news? You don’t have to go through the same struggle. Automating your EHS processes can happen seamlessly. You’re not starting from scratch, you’re equipping your teams with smarter, simpler tools they’re already prepared to use. The end result will be fewer frustrations, easier and clearer reporting processes, and a workplace safety culture that literally builds itself—from the floor up.
If your manual processes cause more groans than gratitude among your safety teams, maybe it’s time to clear out some clutter. Take it from me—someone who’s seen both sides of the automating fence. Invest a little in digital safety systems designed around your team’s existing workflows, and you won’t have to work hard persuading your shop floor teams to adopt safe behaviours—they’ll naturally embrace them.
Here’s to safer workplaces, less frustration, and automations that empower people—not replace them.
If you’re anything like me, you’ve seen your fair share of near-misses across the production floor. Thankfully, nothing serious happened, but every single near-miss is a crucial lesson waiting to be learned. I’m embarrassed to admit that back when we were relying solely on manual reports and paper forms, these close calls used to fill me with dread rather than encouragement for improvement.
Let me paint you a picture: imagine it’s a chaotic Wednesday morning on the factory floor. An employee narrowly misses a collision with a forklift. No injuries, but hearts are racing, and the adrenaline is palpable. The employee catches their breath, heads into the office, grabs a clipboard—and that’s where the drama begins. I noticed a familiar look on their face: frustration mixed with annoyance at yet another tedious task. That clipboard could very well have had ‘ignore me until later’ stamped onto it in bright red letters. Surely, health and safety shouldn’t feel this daunting or, worse still, ignorable?
It didn’t take long for the penny to drop for me. I realised that manual near-miss reporting, while necessary at the time, was adding more friction than function. Employees were tasked with handwriting forms, chasing down busy managers for signatures, and filing the reports away in overloaded cabinets, rarely to be seen—or remembered—again.
I confess that at first, I thought my people were simply disengaged or, worse yet, lazy. I quickly learned that wasn’t the case at all. Truthfully, the manual reporting process we’d put in place wasn’t easy or intuitive and didn’t contribute meaningfully to the daily flow of work. This was my moment of clarity: if a safety process is more cumbersome than helpful, people will inevitably resist it or shortcut it. After all, everyone’s goal is to be productive, efficient, and safe, not bogged down by paperwork dramas.
Let’s be clear—safety reporting is essential, but if the tools and processes we provide slow down our people or deter their engagement, it’s defeating the entire purpose. Manual reports created unnecessary delays and miscommunications, allowed crucial details to fall through the cracks, and painted an inaccurate picture of our overall safety culture. Yes, it was embarrassing to realise this—but acknowledging it was an essential first step.
After accepting that our existing manual process was becoming part of the problem, we explored ways to automate near-miss and incident reporting. I’ll be honest, investing in new technology—incident reporting tools and safety report automations—wasn’t something we did lightly, especially when team productivity and morale were potentially at stake.
However, the transformation that followed was genuinely eye-opening. Implementing a digital health and safety automation system allowed our team to quickly and easily record near-misses from any device on the shop floor. Instead of clipboards ignored in a corner, we created a simple, user-friendly mobile app that made reporting fast, intuitive, and painless. Suddenly, reporting a near-miss was less an inconvenience and more an empowering responsibility.
We quickly saw more comprehensive near-miss reporting. Employees, recognising that their input was valued and easily actionable, began to report more often and with greater detail. Automating the system didn’t overwhelm us with excessive paperwork; quite the opposite—it gave us actionable visibility into potential risks before they turned into serious incidents.
This shift was not just logistical—it caused a subtle but powerful change in mindset. Now employees saw health and safety processes as supportive, collaborative, and productive rather than bureaucratic annoyances. Reports became conversation starters, opportunities, even moments of team pride, rather than dreaded chores.
The change didn’t stop at improved reporting—we saw genuine long-term improvements in how our workforce perceived safety overall. Our improved reporting data now helps management spot trends quickly and implement proactive changes rather than simply reacting to incidents after they occur. Because automated reports feed immediately into dashboards and analytics tools, leadership became more informed and confident in making better health and safety decisions more rapidly.
Crucially, automating near-miss reporting empowered our employees by placing safety firmly into their daily workflow. It eliminated the friction of outdated systems, allowing them to contribute easily to a safer workplace. Our once-reluctant team members became active advocates for safety. They took ownership of their roles in keeping themselves and their colleagues safe, leading to fewer near-misses—and critically, fewer actual accidents.
If there’s one positive takeaway I’ve learned from this experience—beyond the value of automation—it’s the power of respectful reflection. Sometimes, we must swallow our pride and take a hard look at our established habits and practices. If a system or mindset doesn’t serve your people positively, have the confidence and humility to improve it. Implementing automation gave us more than just faster reporting—it gave our team a lasting confidence in the value of safety itself.
Let me ask you a simple yet provocative question: as a safety manager in manufacturing, how much time do you spend weekly sifting through paperwork, chasing forms, and manually inputting data into spreadsheets? You might shrug it off as part of the job—after all, meticulous record-keeping is standard practice in our industry. But have you ever paused to consider what this manual routine is really costing you?
This is not a trick question. A while back, I asked myself exactly the same thing, admittedly somewhat reluctantly. Truth is, we’re all creatures of habit. But when I finally did the maths, the answer stunned me—my outdated paperwork rituals were costing me roughly 10 productive hours every single week—hours that could’ve been better spent fostering proactive safety practices, training my team, or tackling improvement projects.
Let me take you back for a moment. Before we digitised our safety processes, we did it just like most teams out there—we relied heavily on printed documents and spreadsheets that were sometimes formatted optimistically, sometimes comedically. It felt comfortable and familiar, but when we dared to take a closer look, cracks began appearing instantly.
The main issue wasn’t a lack of dedication or care; my team was—and always has been—incredibly diligent. Yet our traditional approach created hidden bottlenecks. Data collection involved chasing down multiple members on the shop floor, each responsible for filling in paper risk assessments, incident reports, and inspection checklists. These forms then vanished into either cluttered trays or (worse yet) disappeared into some forgotten corner altogether. And when we finally tracked them down, we spent more time deciphering handwriting or correcting input errors than we did actually analysing the data.
I’m slightly embarrassed now at just how normal this chaos once seemed. It made me realise that the hidden cost of outdated manual processes isn’t merely inefficiency: it’s lost opportunity. Every hour spent re-typing poorly written paperwork or chasing unsigned forms was an hour directly taken from my ability to create proactive safety initiatives, interact with shop floor teams, and strengthen the safety culture at its source.
I like practical solutions, not flashy ones. So I’ve always been sceptical of complicated solutions promising magic. However, after venting my frustrations to a colleague, he quietly told me about their team’s shift towards digital safety systems. I’d resisted technology at first—surely it would add complexity rather than reduce it—but curiosity got the better of me.
The truth unfolded remarkably simply through adopting straightforward EHS automation tools. Nothing overly fancy or complicated—just easy-to-use software accessible from mobile devices and desktops. This allowed safety team members and shop floor operators alike to complete inspections, incident reports, near-miss forms, and checklists digitally. Our reports could now be signed-off electronically, timestamped, photo-attached, and instantly uploaded. Suddenly, lines waiting for my office printer disappeared (it now collects dust), and paperwork vanishing acts stopped completely.
What’s more, this digital safety system automatically funnelled incoming safety data directly into our central analytics dashboard, accessible anytime for review. I won’t pretend that changing a familiar workflow was entirely painless and hassle-free–it’s never easy departing from comfortable routines. But once embedded, the process was quicker, far simpler, and made real-time insights instantly accessible to everyone involved in our safety operations.
Fast forward several months and it hit me recently during audits: the question-and-answer part had never seemed easier. I’d always thought audits had to be arduous affairs where I’d spend literally hours preparing the necessary paperwork. Now, armed with our health and safety automation system, audit preparations became painless and—dare I say it—enjoyable.
In fact, auditors even praised our swift access to reliable, up-to-date information and commended our thoroughness in documenting potential hazards and preventative measures applied. If you’d told me a year ago I’d genuinely enjoy audit sessions, I’d have laughed (then sighed deeply and wearily), but here we are. Our compliance improved dramatically, our prepared documentation reassured inspectors immediately. In short, audits were less monotonous and more productive.
Perhaps more significant, however, was the downstream impact on our daily operations. Immediately after we fully implemented this digital system, we spotted trends and highlighted concerns practically on the day they happened, rather than weeks later as previously common. With data readily available, we now had actionable insights immediately in-hand to make informed decisions and implement preventative steps rapidly.
As an added bonus, shop floor operators appreciated the ease and flexibility of using mobile devices, leading to noticeably greater engagement in reporting near misses and other crucial data points promptly. Our incident reporting doubled (in a good way). Although possibly alarming at first glance, it meant we were capturing and addressing incidents promptly, encouraging a proactive reporting culture. Improved availability and reliability of safety data accelerated our internal and external reporting dramatically, thus reflecting genuine improvements in our overall safety metrics.
The moral of this journey? Sometimes our own comfort with familiar manual processes blinds us to hidden costs lurking in our workflows. For years, I’d proudly described our traditional method as “tried and true,” never realising that for complex manufacturing environments like ours, “tried and tired, slowing us down” was more accurate.
By stepping out of my comfort zone and quietly replacing endless printouts with straightforward digital safety systems, I personally reclaimed at least 10 productive hours per week. But beyond recalculating hours, it was about reclaiming opportunity—opportunity to continuously improve safety culture, engage better with our frontline teams, and ultimately optimise our commitment to a safe and productive work environment.
If you’re clinging stubbornly—as I was—not to change a checklist routine that “works fine,” perhaps ask yourself honestly: could a simple, practical health and safety automation contain exactly what you need?
Confronting this one uncomfortable question saved valuable hours per week in my safety management work and, more importantly, it dramatically improved our compliance and workplace safety for the better. Take it from a formerly sceptical fellow manager—moving your safety workflows into the digital age will optimise your operation in ways you might never expect. Try it—you might surprise yourself too.
If you’re anything like me, you’ve probably spent hours meticulously filling out safety reports, only to later discover that no one ever read them. It’s a common issue I’ve encountered throughout my career in manufacturing—reports painstakingly completed, yet ignored, stuffed into a filing cabinet or even straight into the bin. To be honest, there were times when I was tempted to chuck them myself, just to save the frustration!
I remember one particularly grim Tuesday morning, coffee in hand, staring bleakly at a pile of paper reports. Each form demanded the same repetitive information: who was involved, where, what happened, and so on. No one liked completing these documents—not me, and certainly not my team. It felt like a task designed purely to sap enthusiasm and bury real safety concerns in paperwork.
What bothered me was not the paperwork itself, but the fact it actively discouraged honest and prompt reporting of safety hazards. If my team viewed safety reporting as a dull box-ticking exercise, rather than a chance to improve working conditions, could we honestly say we were actively managing our risks?
Reflecting on that frustrating Tuesday, I started asking questions. Why exactly are these safety reports ending up ignored? Was it solely because people found them tedious—or was there something fundamentally wrong with the process?
I quickly realised our traditional, paper-based reporting system was part of a much broader problem. Tracking down safety documents, printing off forms, manually inputting details, physically filing reports…these are not just irritating jobs; they are incredibly time-consuming ones. Worse still, this demands a wasteful duplication of efforts, with the same incidents and scenarios repeatedly logged and re-logged across multiple ledgers, spreadsheets, and filing cabinets.
When I dug deeper, I realised that this wasn’t just annoying—there were genuine financial and operational impacts being hidden here. The time my team spent shuffling paper was costing us real productivity and, ironically, potentially impairing our safety management. Admin overload meant hazards were less likely to be reported promptly (or sometimes not at all). Moreover, when audit time rolled around, hours were lost digging through records that were barely legible or incomplete. That’s not safety management; that’s damage limitation.
And then there was the issue of delayed reactions—issues emerging on the shop floor would often languish in paperwork before anyone acted on them. By the time someone finally spotted a safety trend in the reports (assuming they managed to decipher the handwriting), we might have wasted critical days or weeks before implementing an essential safety improvement.
I knew something needed to change. Not a superficial paper reduction exercise—we needed a fundamental shift in our approach. We moved towards integrated, user-friendly digital safety systems and safety compliance software—a change I’m proud of, and one I’d strongly recommend based on what I’ve experienced first-hand.
The transition wasn’t without its speed bumps. I’m not ashamed to say there was initial resistance: “Another tech gadget shoved our way, just what we need,” joked one of my colleagues. Yet quickly, our team saw it was different. The system wasn’t complicated or overloaded with unnecessary features. Instead, safety report automation was specifically designed to make reporting faster and more intuitive, slotting smoothly into our daily workflow.
Staff could immediately log hazards, incidents, and risks via their smartphone or tablet on the factory floor, rather than having to trek back to the office for paperwork. The software prompted them to enter precisely the details needed, stripping away any unnecessary administrative friction. Because reports were digitised instantly, real-time notifications could go straight to supervisors and managers, keeping us constantly updated about safety developments. I’ll admit, seeing how smoothly that worked was deeply rewarding.
Importantly, we didn’t disrupt the existing workflows people had—we enhanced them. As someone who values practical solutions, I believe your best safety improvements build on your existing strengths and processes, rather than forcing uncomfortable new working patterns onto reluctant teams.
The outcomes speak louder than I ever could. Once our automated system was fully up and running, we quickly began noticing a shift in how our team viewed safety reporting. I heard less grumbling about the process and saw a genuine increase in timely hazard submissions. Everyone understood that this method was quicker and easier, so incidents and near misses no longer went unreported or became buried on clipboards gathering dust.
When you can report efficiently and risk-free, people naturally do it more. I’ve been in manufacturing long enough—perhaps longer than I’d care to admit—and I know one thing for certain: no complex safety protocol can ever replace the effectiveness of a simple, accessible, and hassle-free way of doing things.
Digitising has also cut down dramatically on the direct costs associated with traditional administrative processes. No more searching through piles of paper to find crucial information during audits. Reports automatically compile, categorise, and trend safety data—drastically cutting admin downtime during assessments. Safety is no longer a reactive, retrospective headache, but something proactively monitored, managed, and improved upon in real-time.
And rather satisfyingly, my Tuesday mornings now look a whole lot better. Instead of battling through forms, I can now spend that precious time analysing actionable insights and making timely, productive safety decisions. I’ve reclaimed valuable hours back into my working week, and stress levels across the entire team fell markedly afterwards. The smiles I get when safety audits come around don’t feel too bad either.
If your experience mirrors mine, you’ll understand there’s real power (and a sense of personal pride, if I’m honest) in moving from inefficient, frustrating systems to slick and practical automated solutions.
No safety report deserves the bin. When our processes no longer hinder our purpose, but actively support it, the safety culture we all push for becomes not just possible, but inevitable. I learned this the long way round—but trust me, the path to improvement really was simpler than I thought.
Let me take you back a few years to the shop floor, late on a Friday afternoon. I clearly remember wrapping up my day and thinking everything was under control when suddenly the phone rang. It was our Safety Manager; the stress in his voice was hard to ignore. “We’ve missed something,” he said. It turns out, a crucial safety incident that should have been reported two weeks earlier fell through the cracks. You guessed it—a mistake buried deep in our beloved spreadsheet.
This spreadsheet had served us well—it was comfortable, familiar, and, let’s face it, cheap. But its limitations had finally caught up with us. A single missed entry had rippled through our entire safety reporting and compliance process. The subsequent scramble—to find records, clarify details, and manage an urgent meeting with regulators—remains one of my least favourite memories in manufacturing management.
We didn’t fully appreciate the extent of the damage a traditional, outdated safety reporting system could cause until that day. It’s easy to dismiss minor errors—after all, humans make mistakes. But when those mistakes compound, consequences become severe and tangible.
From a human perspective, anxiety soared. Our safety team faced intense pressure and longer working hours to untangle the mess. Operationally, hours upon hours were wasted piecing together events, clarifying timelines, and coordinating cross-departmental resolutions. Supervisor time, technician time, admin hours—these are valuable resources we cannot get back.
Financially, the impact was sobering. The fine we faced wasn’t a slap on the wrist; it was thousands of pounds—money we could have better invested in new equipment, training, or team development. But perhaps more painful was the hit to our reputation. Scrutiny from governing bodies increased significantly, making it clear we had lost some of their trust.
When the dust settled, our team sat down to analyse where we’d gone wrong. It was a hard reflection, one where ego had to take a backseat. Was relying on spreadsheets truly sustainable? Clearly not—we needed a more robust solution.
That’s when we discovered the power of automation through dedicated safety compliance software. It might sound a little dramatic, but the change was transformative. I won’t glorify the solution—it was simply practical and effective. By implementing a digital safety system, we ensured automatic, accurate documentation, prompt reminders, and real-time reporting—not dependent on human memory or email chains.
Instead of spending hours sifting through forms or cross-checking Excel formulas, our safety team now had data at their fingertips—in clear dashboards that showed the status of incidents, overdue tasks, and compliance standards. More importantly, responsibility became clear and transparent. Alerts flagged any missed safety reports instantly, ensuring action could be swift. And, of course, no more missed deadlines or fines.
The beauty of moving away from traditional spreadsheets to automated safety report systems isn’t just about avoiding fines—although, let’s be honest, that’s a big plus. It’s about a cultural shift within the organisation, where accountability and accuracy become ingrained in daily practices. Safety isn’t something we’re constantly chasing—it’s proactively managed and effortlessly tracked.
Long-term, this new approach gave our team peace of mind, knowing our safety processes are reliable and audit-ready at any time. Compliance became less of a stressful priority and more of an everyday norm. We also witnessed a quieter benefit—morale improved. Our safety professionals felt better supported, more confident in their work, and more focused.
Through automating our reporting and compliance processes, we’re now investing our time, money, and energy in preventive practices, training, and improvement initiatives. No one misses the spreadsheet. Well, maybe except for nostalgia—but I’ll happily trade nostalgia for safety anytime. If you’re still stuck using outdated spreadsheets for safety reporting, I’d strongly recommend exploring digital safety solutions. It’s a practical investment—and it just makes sense.
In my experience managing safety across manufacturing sites, one thing I’ve learnt the hard way is that an outdated Environment, Health and Safety (EHS) process is more than just an irritation—it can become an invisible chain holding us back. Don’t get me wrong, I know how tough it can be. You try your best to stay compliant, keep people safe, and manage a dozen other day-to-day priorities. Before we established clearer and smarter systems, our EHS procedures used to consume endless amounts of time through repetitive tasks like manually updating safety reports, paper-based inspections or chasing down checklists around the workshop. It felt like running on a hamster wheel—exhausting, inefficient, and demotivating for everyone involved.
We realised our processes were holding us back whenever we faced an audit or an incident. We constantly scrambled to provide documentation and evidence, leading to reactive firefighting rather than proactive prevention. Our shop floor teams were frustrated with checklists that didn’t fully reflect their tasks, hazard reporting that felt overly complex, and managers spent far too much time sifting through paperwork instead of identifying genuine areas needing attention. Most alarmingly, the sheer administrative burden distracted us from truly observing and acting on genuine safety risks, creating potential blind spots across operations.
Unfortunately, our experiences aren’t unique—it’s widespread and only getting more costly. According to a recent UK Health and Safety Executive (HSE) report, workplace injuries and illnesses cost UK businesses £18.8 billion each year. Equally concerning, in the USA, OSHA estimates businesses spend around $1 billion per week on workers’ compensation alone. Those numbers quickly added some much-needed context to our internal frustrations and provided a real impetus for change. It gave us both the awareness and urgency needed to seriously review our workflows.
Furthermore, research has shown repeatedly that workers find repetitive paperwork demoralising—76% of EHS and operations professionals in one US-based survey said managing paper-based safety records was among their biggest frustrations, reducing their overall workplace engagement and productivity. Clearly, inefficiencies aren’t just minor irritations. They impact employees’ morale, harm productivity, create compliance risks and strain any business’s bottom-line—the very definition of being held back by a broken process.
I understand if the very term “automation” may initially prompt raised eyebrows. When I first thought about automating our operations and safety workflows, I held concerns too—would this add more complexity, alienate frontline teams, or introduce new forms of failure? However, I’ve come to realise automation isn’t about removing the human element. Rather, it’s about removing repetitive manual tasks so teams can spend their energy more effectively on safety management, risk observations, and addressing true hazards.
Digitising safety reports, automating EHS checklists, and deploying streamlined tracking systems made compliance tracking and accurate reporting a genuinely straightforward process, freeing people up for tasks only humans can do best—like observation, decision-making, coaching, and communication. Technology isn’t about replacing dedicated safety staff or bypassing thoughtful oversight; instead, it enables EHS teams to spend their time proactively managing threats, educating employees and identifying risks earlier before critical incidents occur.
In short—automating parts of your EHS reporting isn’t “nice-to-have.” It quickly becomes mission-critical in reducing frustration, streamlining compliance and ultimately ensuring everyone remains safe on your shop floor.
I understand that seeing evidence matters most, so here’s how automation has genuinely transformed workflows I’ve managed.
History taught me the importance of accuracy and speed when it comes to audits or inspections. We’ve all scrambled through filing cabinets or email attachments, searching for an updated inspection checklist for compliance checks, haven’t we? Automating and digitising our EHS checklists means inspectors and auditors now directly access accurate, up-to-date safety checks stored securely online, anytime and from anywhere. Sign-off verification now takes seconds, not hours. No more chasing down paper reports or wrestling photocopiers—just clear, verified documentation ready whenever needed.
One significant example I regularly share within our teams is around digitising hazard reporting. Frontline workers previously struggled documenting hazards as they occurred on paper forms, which inevitably led to under-reporting or delayed responses. Implementing dedicated digital platforms and apps streamlined this workflow dramatically. Workers on the shop floor now simply open the app, snap photos or select hazard details, and submit reports instantly. Automated alerts pinging responsible leaders keep response times incredibly quick—no hazards overlooked, no paperwork piling up or neglected.
We also automated corrective actions and close-out workflows following inspections or audits. Previously, following an audit involved cumbersome manual checks and routine follow-ups, potentially allowing important issues identified to persist. Automating corrective action follow-up meant clear accountability and faster resolution. With automatic reminders sent to the owners of these actions, management has visibility of bottlenecks or overdue issues in real-time.
Most importantly, automating incident reporting workflow allowed us to swiftly investigate underlying causes and roll-out preventive measures quicker. Investigations became fact-driven and systematic rather than dependent purely on memory or hurried handwritten statements. Stakeholders gain visibility sooner and respond accordingly, substantially reducing reoccurrence rates of incidents or near-misses. Outputs of automated processes provide invaluable trend data, allowing us to spot emerging issues and create targeted training quickly.
We’ve always held pride as manufacturing professionals in our ability to adapt and learn from our challenges, not only producing value for our companies but protecting our workers every day. Digitally transforming our EHS process hasn’t just helped us eliminate time-consuming inefficiencies—it has empowered teams to proactively improve safety culture, continually raising the bar on well-being standards.
If any of these signs sound all-too-familiar, perhaps it’s time to genuinely reconsider if your existing EHS processes are holding you back. Take it from someone who’s felt the sting: automating isn’t simply about keeping up with trends but about proactively empowering your teams and protecting your most valuable asset—your people.
I’ve been there myself—standing on the shop floor, clipboard in hand, thinking “there has to be an easier way”. Environmental Health and Safety (EHS) processes exist to keep your workplace safe, compliant, and efficient. Yet often, these very processes become hidden anchors, quietly holding back productivity, engagement, and morale. If you’re spending more hours poring over paperwork and chasing signatures than actively managing safety, it’s a strong sign something needs to change.
Let me put it frankly: safety isn’t negotiable; it’s mandatory. But when compliance and routine EHS checklists become so cumbersome that they detract from meaningful safety improvements, it’s the clearest sign your EHS process isn’t exactly working for you any longer. I’ve lost track of the number of hours our team sacrificed to gathering, validating, and manually entering data—only to realise the entire process had drifted away from the meaningful actions we first aimed for. There was nothing humble about wasting valuable talent wrestling paperwork into compliance. And it certainly wasn’t smart business.
From experience, it’s usually not your team’s willingness that’s the issue—it’s the systems holding them back. The more complex and fragmented your safety assessments or inspections become, the more likely you’ll encounter missed opportunities to catch near-misses or hazards before they escalate. To genuinely elevate your shop floor’s health and safety culture, you must first face the truth about processes designed decades ago in far less demanding working realities. I’ve seen enough failed paper trails and stalled audits to know it: an outdated EHS process chokes innovation and squelches the agile responsiveness our modern manufacturing environment demands.
If my humble lessons sound familiar, it’s because many of us share this challenge. According to a recent industry survey, organisations relying primarily on paper-based EHS checklists in the UK typically experience compliance reporting accuracy below 70%. That’s downright unsettling, considering how critical accuracy is when lives and livelihoods are at stake.
Another telling piece of evidence: a Health and Safety Executive (HSE) study highlighted that businesses manually managing risk and safety documentation waste approximately 15-20% of their safety team’s working hours. That’s literally days every month that skilled experts spend tied up in redundant paperwork, instead of proactively managing safety improvements and training staff.
It’s hard enough to justify the delays and headaches paper trails cause—let alone stomach the potential costs. The British Safety Council estimates workplace accidents equate directly to lost productivity of around £15 billion a year across UK industry. Inefficient or inaccurate safety processes aren’t just frustrations; they’re costly and dangerous bottlenecks. If your gut feeling tells you there has to be a smarter route, rest assured: the data wholeheartedly agrees.
All right, let’s get a little savage here without stepping out of line: If you’re still exclusively clutching paper checklists, you’re essentially trying to WhatsApp with a rotary phone. I’ve felt the Catch-22 myself—aware improvements are necessary but unsure where to even start. The answer I found—and that many in our industry are now adopting—is digital automation.
Digitising safety reports isn’t about jumping on the trending tech bandwagon. It’s about using proven technology to free professionals from manual, repetitive tasks, so they can focus on impactful, practical improvements that genuinely move the needle. After deploying automated EHS reporting, I’ve seen dramatic improvements: clearer incident reporting, deeper operational insights, predictable audit trails, and even a measurable lift in staff morale. It enabled my team to return their attention to truly making our workplace safer, instead of just proving compliance was met last month.
With automated tools that sync real-time safety data into actionable reports, you gain transparency over your entire operation. You shift from “chasing down those last three signatures” to predicting hazards, spotting trends, and stopping safety risks before they materialise. Automation’s real power lies in enabling swift responsiveness—allowing your EHS experts to anticipate, not just react.
To ground my own optimism in reality, here’s how automation practically improved our EHS procedures, free from jargon or fluffy hypotheticals.
One common area of tired frustration was routine safety checklists. Previously, technicians would spend hours logging inspections on printed EHS checklists. Errors were common, duplicates frequent, and fixing issues required retracing confusing paper trails. We implemented cloud-based, digital checklist solutions that technicians accessed directly from tablets on the shop floor. Inspection data is instantly stored, easily accessed, and transparent in real-time. Automated notifications alert our teams immediately when inspections were incomplete or when problematic trends appear. The manual chase became a distant memory—and overnight, employee engagement with these critical checks improved dramatically.
Incident reporting also transformed dramatically. Previously, near misses or hazards often went undocumented simply because the reporting process was tedious, slow, and filled with paperwork friction. Digital cloud-based solutions streamlined the entire process. Team members quickly capture incident details, photos, and videos via mobile devices, ensuring accurate records without fuss or delay. The ease of use dramatically increased the quality and quantity of near-miss reports, giving us far-reaching insights that enable proactive problem-solving and preventative action.
Audits—which nobody truly looks forward to, admit it—also rapidly improved. We moved to an automated solution that digitally catalogues compliance documentation, reports, and inspection records. Practically overnight, audit preparation evolved from days of chaotic scrambling to mere hours of organised routine. The auditor even complimented our preparedness— pure poetry to an EHS manager’s ears, trust me. Automation showed us clearly that organised documentation doesn’t have to be soul-destroying.
Workflow automation similarly bolstered our training and compliance accompaniments. By instantly flagging when team members were coming due for safety training renewals or qualifications, automated notifications replaced complex spreadsheets and exhausting administrative checks. Training gaps shrunk significantly, compliance became second nature, and morale improved as staff realised learning wasn’t an exercise in frustration.
These rather ordinary improvements don’t sound dramatic—but frankly, that’s part of their beauty. Efficient, automated systems quietly remove friction, allowing EHS professionals to focus on genuine acts of leadership. Safety becomes proactive, not reactive. Your team’s expertise regains its rightful significance, liberated from the boring tedium of manual checks and paperwork management. And the frontline staff who keep our workplaces thriving have better tools to maintain their own safety, expertise, and productivity.
I’ve learnt first-hand—through successes and frankly, the odd dumb mistake—that sometimes the scariest risk is sticking too rigidly to what worked “well enough” five years ago. If your EHS process has become a sticking point rather than sharp advantage, it’s time to reflect honestly about updating your approach. Digitising your safety reports and automating your routines doesn’t have to be a daunting task; in truth, it’s the lifeline your safety culture and productivity desperately need.
Making this change not only enhanced safety dramatically—it freed my team’s capabilities and restored energy and purpose to our EHS processes. So trust me when I say that admitting to your EHS process problems and then fixing them with automation isn’t weakness. It’s savagely sensible, honestly humble, and unquestionably smart business.
Here to ensure future incidents are prevented by delivering robust compliance tracking systems.