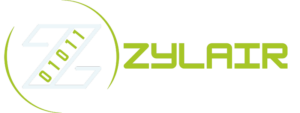
Automating Risk Reduction
Imagine a job where the mundane, repetitive paperwork is reduced, and stats just…appear!
Imagine a job where the mundane, repetitive paperwork is reduced, and stats just…appear!
I’ll be straight with you—in my early days as an Engineering Manager, nothing filled me with dread quite like the phrase “health and safety reporting.” If you’ve ever spent hours chasing paperwork, decoding handwriting worthy of a doctor’s prescription, or hunting down that essential piece of misplaced documentation, you understand exactly the frustration I’m talking about.
I remember standing in front of my team during a shift handover, asking for a recap on an incident. The response? Blank stares, shoulder shrugs, murmured guesses. Not because the team didn’t care—but because our reporting system was clunky, overly complex, and manually intensive. We were relying on clipboard checklists and spreadsheets scattered across multiple desktops. Despite good intentions, important safety observations simply slipped through the cracks. It wasn’t just embarrassing—it left me anxious, knowing our well-being, compliance, and reputation could depend on this cumbersome system.
Let’s get real. Old-school reporting isn’t just a daily bother—there are tangible consequences to leaving manual systems unaddressed:
People Impact: Safety professionals like us genuinely want our colleagues to get home safely every night. But when vital incident data gets lost or forgotten, we’re rolling dice with people’s well-being. One unchecked hazard, one trend that slips notice, can quickly escalate into a devastating incident. Workers who’ve felt ignored will naturally become disengaged. Trust erodes. Safety suffers. A team that doesn’t feel secure can’t perform at their best potential—which hurts all of us.
Financial Impact: Even experienced managers sometimes overlook how manual inefficiencies quietly drain department budgets. Duplication of effort, administrative labour hours, fines from missed compliance requirements—I learned firsthand these aren’t minimal expenses. There was a time we spent thousands annually trying to reconcile errors due to manual reporting. That budget could’ve been directed towards training or robust preventive measures—efforts that truly matter in the long run.
Operational Impact: Every time we’re searching for information rather than acting on insights, we’re allowing inefficiencies and unnecessary risks to persist across our sites. This holds true whether you’re in Manchester, Milwaukee, or anywhere else. Health and safety managers can’t be everywhere at once, and neither should they try to be. When teams wrestle with cumbersome paperwork instead of quick, intuitive digital systems, the operations grind slower. However subtly—it chips away at productivity, engagement, and ultimately, competitiveness.
The good news? This isn’t a problem that requires sweeping, disruptive change—it’s a tweak, not a rebuild. I’ve observed time and again that integrating lightweight, intuitive safety compliance software into existing workflows can quickly turn things around. Digital incident reporting tools might not be the glamorous stars of the health and safety world—but in my experience, they’re the unsung heroes that make a tangible difference.
We implemented simple, user-friendly health and safety automation within our existing system. What I appreciated most—it was adaptable enough to allow workers on the floor to log incidents or observations right from their mobile device. Within moments, a simple risk observation could appear across multiple dashboards, alerting the right teams for review. No complex training sessions. No system downtime. No need to reinvent the wheel.
The key I discovered was integrating incident reporting software seamlessly into my team’s existing day-to-day life, minimising disruption. Today’s thoughtful automation solutions let people do their jobs without jumping through paperwork hoops—it empowers them by removing burdens, rather than adding new ones.
The change, in retrospect, was staggering—though at the time it simply felt logical and incremental. After implementing automated incident reporting, we began to see transformation in three core areas:
Audit Confidence: Audits became simpler—and far less stressful. Before, it was an anxiety-inducing scramble to track down documentation, incident notes, and compliance records scattered across emails, clipboards and desktops. Now, a single dashboard meant I had accurate records of every observation, every incident report, every follow-up action. Auditors walked away happy (imagine that)—and more importantly, we were genuinely confident our documentation lined up across the board.
Faster Reporting Speed: Because our incident reporting tools fed directly into live dashboards, updated incident logs were instantaneously accessible. Reporting formally became something we could practically do at the touch of a button rather than scrambling to piece together disjointed information. Instead of wasting energy manually preparing reports, we could dive directly into taking informed, corrective actions.
Safer, More Engaged Teams: Safety metrics, over time, improved—not surprisingly because staff at all levels felt empowered to flag potential hazards or report minor observations without hassle. The simpler we made reporting, the higher engagement we saw, and the more accurate insights became. Fewer hazards persisted unnoticed, and the culture of safety visibly strengthened among the team. Engagement, morale, and safety became self-reinforcing.
Truthfully, I regret not adopting automated safety compliance software earlier. I’ll openly admit—I once dismissed health and safety automation as another unnecessary piece of IT that would complicate an already overwhelming workload. Yet looking back, resisting modernising our incident management might have cost us both financially and operationally—and even worse, jeopardised our workers’ safety.
Let’s align the responsibility of health and safety management with the smart tools and tech readily available today. Practically speaking, incident reporting tools allow us to work smarter without working harder. If your gut tells you manual spreadsheets and clipboards are holding you back—I guarantee you’re right from experience. Automating safety compliance might just be the most undervalued decision you’ll make to help yourself, your team, and your workplace thrive.
I vividly remember the morning I walked into the factory to find the Health and Safety Manager with a rather grim expression, clipboard in hand. Like most manufacturing professionals, safety audits weren’t exactly the highlight of my week. Necessary, sure, but I used to dread the countless hours spent chasing paperwork, tracking down missed checklists, and politely ‘nudging’ team members to capture critical data. But that morning turned out to be my wake-up call.
It seemed one simple machine safety check had been inadvertently missed—nothing inherently unusual. But this time, that oversight nearly had serious consequences when a critical emergency stop system failed during a routine operation. Thankfully, quick thinking from the operator avoided injury, but it became alarmingly clear: our process was broken and something needed to change.
Upon reflection, the problem wasn’t the staff or their training. Our safety processes had become victim to their own complexity. Paper checklists were misplaced or left incomplete. Manual input errors compounded, wasting hours each week. In the end, a variety of reports from audits ended up neglected in a dusty filing cabinet, until something urgent forced us to track them down.
As Engineering Manager, I realised we were wasting valuable productivity chasing documentation instead of addressing real hazards. Every hour spent deciphering hastily-written forms and checking stacks of audit results could have been invested in operational improvements, staff communications, and genuine risk management.
It got me thinking: surely in the age of Industry 4.0, we weren’t still relying on clipboards and elastic bands to keep everything compliant? The hidden cost was enormous—in terms of human risk, the sheer stress levels, labour inefficiencies, and even potential liability. Our manual, outdated method was more than an inconvenience; it was an unseen barrier that stopped us fully committing to proactive safety and continuous improvement.
I knew we had reached a tipping point—we had to embrace technology. And if you’re thinking automation is just another fancy buzzword or overly expensive system—you’d be right to be wary. For too long I’d been sceptical myself, imagining complicated software that no one would actually bother using. But when I finally implemented a practical and straightforward EHS automation solution, it immediately clicked into place.
Specifically, we deployed a simple digital safety compliance software. It sat comfortably within our existing workflows, accessible via smartphones and tablets that our team were already familiar with using. No steep learning curves, no frustrating training hurdles—just clear digital checklists, automated reminders, and effortless data logging. This allowed every safety audit, check and observation to feed straight back into a real-time dashboard. Finally, we could instantly spot trends, issues, and escalate issues immediately, not two weeks later.
Your shift supervisor spots a damaged guard rail? They photograph and log it in seconds. An operator notices increased friction in machinery? They raise immediate action via an intuitive form. Automated alerts go straight to relevant Maintenance or Health and Safety team members—no extra emails needed. The dreaded paper chase was banished overnight.
Adopting automation didn’t mean costly, complex systems I’d once feared. Instead, it slotted seamlessly into our work routines, almost invisible in its simplicity, but exceptionally powerful in its impact. Safety had finally joined the digital age.
What happens when you finally eliminate the confusion, delays, and stress of manual safety audits? Well, for starters, you regain precious hours for yourself, your staff, and the Health and Safety team.
Where previously audits took hours of preparation, chasing paperwork, and deciphering scrawl-like handwriting, now we performed them smoothly within our usual operating rhythms—taking mere minutes rather than hours. Automated reminders and digital checklists instantly created clear, traceable, actionable audit trails.
Additionally, we saw a tangible reduction in near-misses and incidents. Operators could report safety concerns immediately, resulting in quicker preventative actions. We finally had a proactive process rather than a reactive scramble.
But most of all? I noticed genuine team morale and engagement improvements. Nobody was rushing around last minute, worrying they’d missed something critical that would land them—or the whole organisation—in trouble. There was a quiet confidence building in knowing we had a complete overview of all hazards, audit results, trends, and corrective measures right under our fingertips.
Automation freed our time, reduced hotchpotch manual work, eliminated repetitive, boring admin—and dramatically cut down stress levels. Today, audits are no longer something I dread but something that genuinely adds value. We can focus on proactive solutions and maintaining consistent safety standards, instead of firefighting hidden issues.
If you’re currently still stuck running around with checklists, breaking into sweats over missed paperwork, or facing the unnerving reality of incidents slipping through the gaps, perhaps EHS automation can be your wake-up call too. Because frankly, your job is stressful enough already—without clinging desperately to outdated methods the manufacturing industry has thankfully long outgrown.
Together as manufacturing engineers and Health and Safety Managers, we owe it to our teams to learn from past oversights. Luckily, the game has changed—and you don’t have to dread another audit day again.
I’ll admit, not so long ago I was pretty proud of our ‘comprehensive’ safety checklists and manual incident reporting. I’ve spent entire afternoons chasing down paper forms, deciphering scribbled handwriting, and coaxing supervisors to update endless spreadsheets. Somewhere between “that’s how we’ve always done it” and “we’ll get around to digital later”, I realised our approach wasn’t really keeping us safe—it was simply creating busy work.
So let me pose the question a bit more bluntly: Does your current safety workflow genuinely enhance safety on the factory floor, or does it just check compliance boxes and pile paperwork onto your team? If you paused and sighed, believe me, I’ve been there.
The inconvenient truth about manual reporting and paper-based safety checks is that, despite our best intentions, they’re vulnerable to inconsistency, mistakes, and oversight. They might feel reassuringly familiar, but that’s no excuse when it comes to keeping our teams safe and our processes compliant.
From experience, the consequences of clinging onto outdated safety reporting methods can quietly add up, both in visible and hidden costs. Let’s break it down clearly:
Human Cost: Manual methods rely heavily on individuals who, despite their best intentions, inevitably tire, rush, or occasionally cut corners—because they’re human. Missing an inspection here, overlooking a near-miss report there—these slips mean hazards can easily fly under the radar until they result in injury or worse. I’ve seen talented workers injured from scenarios clearly preventable with a swift, accurate escalation or earlier intervention. Every avoidable incident is a human cost too big to bear.
Operational Impact: Inconsistent safety procedures slowly chip away at operational efficiency, too. How many man-hours are lost chasing incident reports, double-checking records, or photocopying and filing documentation? Time your team spends on admin tasks is time they’ve lost for skills training, process improvements, or actual production workflow optimisation. And if you’ve ever spent hours preparing data for an audit (hands raised?), you know exactly the loss of productivity I’m talking about.
Financial Consequences: Add these up to significant financial losses. Workplace accidents and resulting claims, regulatory fines from missed compliance deadlines or incomplete documentation—they all directly impact the bottom line. Indirectly, inefficiencies mean higher labour costs and wasted resources. Suddenly, the cost of “sticking with the status quo” starts to stack up alarmingly.
I’m not saying manual reporting can’t “manage” the occasional problem—but when you start to consider the cumulative effect, it really isn’t worth the risk it represents. It’s not only inefficient, it’s subtly dangerous.
Last year we decided we’d had enough and started exploring practical safety improvements centred around automatic reporting and data analytics. Here’s what finally worked for us—a simple yet powerful EHS automation solution that streamlined our processes without creating added overhead.
We implemented a cloud-based digital platform specifically focused on safety report automation. With easy-to-use mobile and tablet apps, our frontline supervisors and operators could quickly log safety inspections, near misses, or hazards directly from the factory floor, complete with images, videos, timestamps, and geographic locations, all within seconds.
The beauty here? Automation took care of the rest. No more photocopies, no more spreadsheets, and no more chasing staff to complete reports. Alerts and notifications automatically flagged anything requiring immediate evaluation or intervention. Moreover, real-time dashboards allowed managers—including me—to quickly spot emerging trends, perform root-cause analysis, and track resolution actions, all accessible remotely and immediately.
The most significant positive surprise was understanding that introducing automation didn’t need extensive training, technological overhaul, or IT headaches. We chose a simple-to-adopt SaaS tool built specifically for manufacturing safety environments, meaning implementation took weeks, not months, and the learning curve was refreshingly short. And that meant getting our team engaged and onboarded was a practical reality rather than a drawn-out process.
It’s amazing what clarity, simplicity, and ease-of-use can do for compliance. Within a few months of switching to automated safety reports, we saw tangible improvements across the board.
Firstly, reporting accuracy and frequency greatly improved. Rather than scribbling notes on scraps of paper between tasks, our staff could quickly tap on handheld devices and get back to what they do best. The simplicity itself became incentive enough to report proactively rather than putting things off. Because data was digital, records were always complete, legible, and auditable—no more guessing or second-guessing what happened during last week’s site walk-through. It also subtly removed excuses from the team (I’m sure you’ve heard plenty—”lost my clipboard”, “forgot the form”, “too busy”). Automation took those off-limits, making compliance straightforward instead of cumbersome.
Secondly, the transparency of the automated system drove accountability. Managers and team leads were fully aware of what’s expected, seeing real-time information on their own performance—this made complacency harder to conceal. Risk patterns became visible earlier. Everyone started responding faster to emerging safety concerns, reducing near-misses, injuries, and potentially disastrous events. The reductions in incidents, downtime, and paperwork each month were not just figures on an operation dashboard—they represented the improved health and wellbeing of actual human beings.
The biggest surprise was the seamless adoption. Far from rejecting the new system, our team embraced it precisely because it liberated them from paperwork drudgery. They instantly recognised value—the automation gave them the time and freedom to focus on practical actions that really boosted safety and productivity. And to be frank, the grumbling from earlier procedures faded quickly. After all, it’s impossible not to prefer practical, fast, engaging processes over outdated bureaucracy.
So, if you’re still clinging onto the old manual workflow for managing safety—trust me, I’ve walked in your shoes and made those same mistakes. Optimising health and safety doesn’t actually have to be complicated, costly, or painful. The right automation isn’t about control or appearances—it’s about freeing your staff to do their best and safest work while giving you real-time, reliable insights.
Health and safety automation, specifically safety report automation and EHS automation, has transformed how we work. It’s not about chasing paperwork; it’s about keeping workplaces safer more effortlessly. Imagine a system that delivers compliance, adoption, clarity, and peace-of-mind without headaches or extra overhead. Isn’t that exactly what all of us safety champions want?
If you’ve ever managed health and safety on a factory floor, you’ll know the dread of incident reporting all too well. For me, it was those Friday afternoons, feeling defeated, filling out yet another manual report form with details I’d already jotted down twice that week. Stacks of paperwork piling up on the corner of a well-loved desk; chasing down handwritten reports from the shift supervisors; emails back and forth clarifying scribbled notes in the margins—it’s enough to test even the steadiest nerves.
Back in the day, we used to think this was just part of the job. Mantra-like reassurances echoed through the plant: “Safety comes first,” we’d tell each other, “records are just part of the game.” Well, true enough, safety does come first—but we were missing a crucial point. Wading through reams of paper doesn’t make us safer; it distracts us from actually keeping the floor incident-free. And worse, manual reports eat into valuable time which should go towards making proactive improvements.
The trouble, I soon realised, was more than just the frustration of paperwork; manual safety reporting and incident tracking introduced friction into every single aspect of health and safety management. Here’s an example I’m sure some of you can relate to:
I remember clearly, one afternoon after a minor forklift incident, spending precious hours trying to decipher hastily jot-down notes on a muddy, tea-stained clipboard. The time ticked by relentlessly as I typed it painstakingly into spreadsheets and reports, re-entering data twice or even three times to meet different reporting requirements. Papers shuffled at safety briefings, late-night panics hunting down forms for audits, and growing doubts about the accuracy of our numbers. In fact, one of the most critical lessons came when we realised our metrics were skewed not because of actual performance, but simply due to incomplete or misinterpreted data.
In short, the manual approach to reporting was actively holding us back. Poor design, inefficient data capture, and challenging steps wasted our time, undermined confidence in our safety compliance, and prevented us from learning rapidly from incidents. The irony is painful: a process meant to protect our people was becoming a risk in itself.
The game-changer for us came only when we finally questioned our assumptions around incident reporting tools and decided to embrace automation. Now, I understand the scepticism. I was there myself. Initially, I worried about complexity, about people resisting change, and about whether we’d realistically see a return on our investment. But here’s the straightforward truth: modern safety compliance software has completely rewritten the story for my plant. And with hindsight, I openly wonder how we coped so long without it.
Today’s digital incident reporting tools are a whole different beast. Where once I was scribbling illegible handwriting, now a front-line operator takes mere seconds to fill an intuitive digital form right from a tablet. Drop-down menus, barcode scanning, and embedded instructions eliminate guesswork. Data validation prevents incomplete submissions entirely. I’ve learnt that if we want workers to accurately and willingly report, our tools simply must be user-friendly. When we introduced our own automated incident tracking solution, reported incidents became more precise and easier to capture—and crucially, we actually began to hear about incidents early enough to prevent reoccurrences.
The automation didn’t just collect data quicker—it automatically fed that data into a centralised dashboard, instantly updating charts and notifying key stakeholders. No more Friday afternoon dread; no more chasing after colleagues for follow-ups. Just accessible, trustworthy information at our fingertips.
The downstream results of our investment in health and safety automation transformed far more than just incident tracking itself. It streamlined our whole approach—from regular audits to management reporting and, most importantly, our site’s overall safety culture.
Firstly, audits became significantly less painful. With our centralised, easy-to-use compliance system, reports are now automatically generated from data captured at source. Before, I’d spend hours compiling documents, cross-checking figures, triple-checking everything to avoid audit embarrassment. Now? Reports are pre-populated, accurate, and entirely auditable from start to finish—which keeps our official documentation watertight and inspectors appropriately impressed, rather than raising eyebrows.
Secondly, the speed of reporting incidents and near-misses took a giant leap—minutes rather than hours or days. For health and safety managers who truly want to drive change, improving this reporting speed allows us to move into proactive mode faster. Rather than spending our afternoons poring over frustrating paperwork, we identify trends—such as repeated near misses in a particular area—and intervene before serious injury occurs. The focus, finally, is back where it should be: continuous and incremental safety improvement.
But perhaps the most noticeable and valuable result is something intangible: improved morale. Your team sees that Management cares enough to invest in a system designed to protect them, rather than burying their efforts beneath stacks of clipboards and reports. Simplifying reporting sends a clear message: “we take your safety seriously—and reporting an issue won’t punish you with extra paperwork.”
We’re no longer drowning beneath redundant tasks; we’re swimming confidently in insightful, actionable data. That frees up safety teams for vital tasks like conducting proactive hazard-spotting walks, engaging with staff about safety ideas, and continuously improving from the ground up. It’s a vast improvement we didn’t even realise was possible—not until we finally ditched manual reports for an automated reality.
So what’s the core insight here, for a busy safety professional like you? It’s deceptively simple, but absolutely crucial: an effective health and safety system should do the heavy lifting for you
Make your environment safer, not your paperwork piles bigger. Automating your incident tracking and reporting isn’t about chasing a fancy new software trend; it’s a practical choice, driven by the urgent need for accuracy, speed and safety culture improvement. In our experience, these automated safety systems genuinely transformed the working day, and I’m confident they’ll do the same for you.
Believe me, the hardest part is just to start—stepping away from familiar but painful old processes and trying something new. Is it scary? A bit. Is it worth it? Absolutely.
Let’s save our frustration for things worth getting frustrated about—not repetitive paperwork tasks we know we can fix. Remember: health and safety automation doesn’t just mean smoother audits, faster reporting, or more accurate metrics—although these alone are more than worthwhile. It ultimately means a safer workforce, better morale, easier decision-making, and more time back in your day. Take it from someone who’s spent enough Friday evenings battling endless paperwork—the modern way is not just easier, it’s undeniably smarter.
As a seasoned engineering manager in manufacturing, I’ve worked alongside enough Health and Safety professionals to know that your role isn’t exactly easy. Safety compliance demands constant vigilance, and incident documentation can quickly spiral into a maze of paperwork and spreadsheets. We’ve all found ourselves down the rabbit hole of manual reporting, spending hours chasing up loose ends, wondering if this is really the best use of our talent and resources.
I’ve been there myself: sticking to processes because “that’s how we’ve always done it,” clinging to spreadsheets because change felt disruptive, and ultimately realising that the supposed stability was holding us back. So, let me put this carefully but bluntly—could it be time we stopped making excuses for an outdated EHS system that’s no longer fit for purpose?
I’ve learned the hard way—the real costs of an outdated environment, health and safety (EHS) system aren’t always immediately visible. It’s tempting to think we’re saving money by holding onto our trusted spreadsheets and manual checklists. But the reality is a little tougher to swallow. The hidden losses run broader and deeper than we realise:
Human impact: Manual data entry, chasing signatures, or transferring incident files might seem straightforward enough. However, these repetitive processes contribute significantly to administrative burnout among your valuable team members, not to mention increasing the inevitable human errors that arise with manual entries. These errors may seem trivial, but one misplaced decimal or overlooked field on incident reporting forms could affect lives on the shop floor.
Financial impact: Think about the hours spent constantly updating, filing, and cross-referencing paperwork. Those are precious hours diverted from more impactful, proactive initiatives that prevent safety issues in the first place. Additionally, incomplete or inaccurate records could mean facing fines during surprise audits or legal challenges—which any seasoned professional knows quickly becomes costly.
Operational impact: A well-run manufacturing operation thrives on clarity, efficiency, and reliable systematic approaches. Sticking to outdated methods inhibits our capacity to quickly analyse incident trends and implement changes that reduce downtime. The inability to swiftly access reliable, real-time safety data can keep managers scrambling. Meanwhile, productivity declines while lost-time incidents and disruptions pile up.
Honestly, we owe it to our team to confront these hidden costs. We don’t have endless staffing, time, or budgets to waste on outdated ways of working.
Let me share a personal experience. Not long ago, our EHS management was still reliant mostly on spreadsheet tracking and paper-based checklists. Sound familiar? We’d dedicated decades to building a solid culture of safety compliance, but the administrative side of incident reporting had stubbornly refused to evolve. We justified our practices, convincing ourselves these methods were straightforward, low-cost, and ‘got the job done’. In reality, we were sending good hours down the drain while stumbling in gathering actionable analytics.
Switching to an integrated, cloud-based health and safety automation platform transformed how we managed it all. Suddenly, our team had closer visibility into real-time issues on the shop floor without waiting for cumbersome manual data-trawling. A simplified incident reporting tool dramatically improved documentation accuracy and made reporting significantly quicker and easier for operators and supervisors alike.
Instead of drowning cartloads of paperwork, my team could invest their attention in proactive safety measures and training programs. Safety shifted from a reactive box-ticking exercise to proactive strategic planning, benefiting operational efficiency, employee morale, and long-term wellbeing. It was genuinely eye-opening to realise how far we’d come simply by facing down our stubborn attachment to outdated processes.
I know—admitting that our formerly solid EHS processes no longer meet the mark isn’t comfortably done; it requires a bit of pride-swallowing. Yet, believe me, once that hurdle is cleared, your whole perspective changes. By embracing modern safety compliance software for incident reporting and data management, you’re not just introducing another technological tool; you’re liberating your safety efforts from operational clutter and freeing up your talented people to focus on meaningful change.
Over time, that positive impact stretches outward. Incident reduction becomes an achievable, trackable goal rather than hopeful thinking. Employee engagement increases as teams realise management genuinely cares about providing them user-friendly and accessible safety compliance tools. Audits become less stressful and significantly quicker because every record is accurately logged and instantly retrievable. In short, by making this switch, we establish a safety culture that’s proactive rather than reactive.
Having walked this path myself, I realise that a modernised approach to managing health and safety doesn’t just fix immediate administrative pains—it makes room to build a more engaged, responsive, and reliable safety environment. Honestly, we can’t afford to remain stuck in spreadsheets forever. So, isn’t it about time you considered whether your current EHS system is holding your people—and business—back?
I clearly recall one particular shift on the production line when I was supervising manufacturing operations back in my early days. Everything seemed fine—until it very suddenly wasn’t. We had a near-miss that put one of our operators alarmingly close to serious injury. Thankfully, no one got hurt that day, but it should have raised all manner of internal alerts, flags, and notifications so we could properly respond and learn from it to avoid similar incidents in the future. It didn’t.
Why? Because the reporting tool we had at the time required employees and supervisors to individually log in and fill out lengthy forms to record incidents. Workers were busy enough trying to keep pace with production targets, and anyone who’s spent time on the shop floor knows that urgency doesn’t always leave rooms and minutes spare to remember usernames, passwords, or multi-step authentication. As a result, the near-miss was noted casually by the team but never recorded formally, meaning valuable lessons went undocumented and unnoticed.
When I reflect back on that seemingly minor oversight—an employee was okay, after all—I’m deeply aware of the hidden costs and risks we unknowingly accepted by not fixing our clunky reporting process immediately. Let’s briefly break these down into three core areas: human, financial, and operational.
From a human angle, consider the trust that was eroded because safety concerns appeared to fall on deaf ears. Seeing management unaware of critical risks didn’t exactly inspire confidence among our talented operators and technicians. Employees expect management teams to proactively manage risks when something comes up. Failure to capture these incidents thoroughly and easily undermines morale and raises frustration levels quickly.
Financially, unreported near-misses or hazards inevitably increase the prospect of real incidents that cause downtime, damage equipment or worse—lead to injuries or workers’ compensation claims. The short-term cost-savings of avoiding action or not streamlining an ineffective safety system pale in comparison to the potential fines, liability, medical and operational downtime incurred by real-life incidents that weren’t blocked by early reporting.
Operationally, ignoring employee-reported near-misses or hazards becomes systemic when reporting is too burdensome. Gradually—and sometimes invisibly—a culture emerges where hazards aren’t proactively acted upon. Employee engagement and productivity can subtly decline, and overtime worker attrition and frustration rise significantly. Worse still, important opportunities for continuous improvement lose visibility as staff become accustomed to inefficient processes and stop trying to improve them.
To address those fundamental issues, I took a practical step and implemented a new form of health and safety automation—a system for reporting incidents that required zero logins or memorising any passwords. Contrary to what some providers may tell you, effective EHS automation doesn’t necessarily entail complex interfaces or multi-layered security controls every step of the way.
We chose a simple, intuitive tool that allowed frontline personnel to report hazards, near-misses, or potential safety improvements quickly and anonymously if they wished. Accessible right from their phones, through a QR code scan or bookmarked link saved on their personal or company device, the reporting page asked straightforward, non-technical questions that operators could answer within seconds—and they never needed to log in. Submitted incidents went directly into our EHS automation platform, where appropriate personnel were instantly notified so quick, informed action could be taken.
Removing these login hurdles created more than just an easier system—it built a trustful flow of communication between front-line workers and the health and safety team. Employees felt heard because we responded to their concerns rapidly. Engagement rates skyrocketed from almost zero incident reports recorded per week to multiple meaningful submissions daily. Those early interventions allowed us to prevent hazards turning into costly real-life accidents.
A good friend and colleague, who had initially opposed these simplified incident reporting tools, once questioned why I insisted on removing log-in barriers, asking if security or accuracy wasn’t lowered. Despite his initial scepticism, the system is now something he regularly champions himself.
We found that by improving employees’ ability and willingness to quickly flag hazards and incidents, we drastically improved our ability to prevent potential safety calamities—avoiding far greater disruptions down the line. Indeed, ease and speed of input translate directly into higher accuracy and greater quantity of valuable safety data.
Looking back, the lesson is clear. If your incident reporting tools place effort before ease, complexity over speed, login barriers before accessible usability—you are unintentionally putting your operation at risk. Simple, frictionless EHS automation tools win every single time, as they remove barriers to reporting, build robust trust between management and operators, enhance employee engagement, and deliver critical safety insights that keep operations up and running smoothly.
So, if you want my advice based on hard-learned experience: Never build (or buy, frankly) EHS or incident reporting tools that require user logins or complicated authentication steps. Complexity is the enemy of responsiveness—especially in health and safety. It’s time to strip out unnecessary barriers. Your employees, your productivity, and your long-term safety metrics will thank you for it.
We’ve all been there: it’s late on a Friday afternoon, the factory floor buzzing with the weekend looming, when a minor mishap escapes our radar. I still remember clearly—the issue was a maintenance safety lock that hadn’t engaged properly. Thankfully, no one was hurt. But here’s the thing: it wasn’t captured or properly reported because the whole team was bogged down in the tedium of paperwork, forms and manual processes. I’m not proud to admit it, but in that moment our old-fashioned approach almost let safety slip through our fingers.
When incidents—even near misses—get missed or overlooked, we’re essentially running on luck. I remember the sinking feeling when I realised the oversight had occurred simply because our reporting relied on memory and a manual checklist that everyone dreaded filling out. How did safety become something to dread? And more importantly, how could we transform it into something straightforward, quick and accurately tracked without hours spent on paperwork?
You know this as much as I do: asking already time-pressured and tired staff to fill paperwork excessively, or to attend yet another full-team meeting, doesn’t endear anyone to the safety culture we’re trying hard to embed. The insights we need get buried underneath mind-numbing form-filling and follow-up emails which, though well-intentioned, often end up as background noise.
In fairness, the challenge here is universal. I’ve witnessed it first hand across multiple manufacturing sites, both here in the UK and when spending time with counterparts across the pond in the USA. When safety feels like extra admin rather than an integrated part of daily operations, buy-in dwindles to the bare minimum. That’s dangerous territory. It leads to incidents being reported late, near-misses forgotten, and employees who understandably struggle to prioritise safety paperwork after a long shift.
And let’s not shy away from this truth—manual, outdated processes inadvertently frame safety as optional or secondary. Even the most committed teams can’t escape the friction caused by paper-driven chaos, clumsy spreadsheets and clipboard-centric handovers.
Here’s a truth I’ve learned repeatedly: often, the simplest solutions have the most profound impact. We piloted a digital approach at our facility that precisely aimed at these friction points—a digital safety system that automated routine safety tasks and reporting. I’m talking about intuitive, no-nonsense safety compliance software that could be accessed easily by operatives on tablets or terminals right on the shop floor.
The change was remarkable. Suddenly, reporting near-misses wasn’t burdensome. Instead of grabbing a clipboard, hunting for a pen (how is it that pens are never there when needed?), and laboriously filling out forms, our operators could quickly tap through a straightforward digital report in seconds. Health and safety automation is not about adding complexity; it’s about stripping back barriers. It simplified the entire process, making it actually possible—and satisfying—to track and manage safety activity instantly.
It wasn’t just near misses that got easier. Routine checks and inspections transformed from dreaded manual tasks into easy, daily habits. Automating safety processes freed up our teams from the sheer frustration of paperwork, empowering them to report early and accurately, catch trends quicker, and intervene before small hazards snowballed into significant issues.
Now I’m not saying that software alone fixes safety culture—that’d be naive. Rather, we’ve discovered that eliminating unnecessary administrative friction brought about a noticeable shift. Teams became more proactive. Not because we lectured from the front of weekly meetings, but precisely because the tasks that encouraged early visibility, fast response, and accurate reporting literally became simpler, faster and more intuitive.
Applying digital safety systems taught us something important. Eliminating friction doesn’t just speed things up—it starts to fundamentally flip employees’ attitudes towards safety itself. People inherently want their workplace safe—the resistance we typically face comes from cumbersome manual systems, not attitudes.
Since moving to health and safety automation, I rarely call all-staff meetings purely for safety reminders—there’s simply no need. Safety is now a natural, integrated routine, and that’s how it should be. Of course, open dialogue and healthy discussion around safety remain essential. Yet, without endless manual checklists and the ever-present dread of complicated audits, these conversations turn productive, meaningful and genuine.
Creating a smoother safety experience pays dividends far beyond influencer metrics or audit trails. We’ve experienced better quality data, earlier hazard spotting, reduced incidents, quicker audits, and perhaps most importantly, an improvement in the overall attitude towards safety. People now trust that the systems we use exist to genuinely support and protect, rather than box-tick or micro-manage. And believe me, that’s an attitude shift you can’t fake.
At the end of the day, if we genuinely want teams to engage meaningfully in safety, we owe it to them to simplify the task. Digital safety systems don’t just streamline operations; they create a practical path towards a healthier, more productive safety culture. And if that saves even one colleague from potential harm, isn’t it absolutely worth making the transition?
I remember clearly a morning several years ago when our team presented our latest health and safety report to our executive team. We were confident we’d captured every possible risk, evaluation, and near-miss incident. But as soon as the session finished, reality landed hard: a supervisor approached me and mentioned several critical shop floor incidents I’d never heard of.
Turns out, our frontline staff were avoiding the clunky, slow incident reporting tools we’d set up—tools that were supposed to keep them safe, not frustrate their day. Later research revealed a surprising statistic I’ve kept front-and-centre ever since: According to the Health and Safety Executive (HSE), over 33% of incidents in manufacturing never get properly reported (UK figures). In the US, OSHA compliance records indicate similar patterns.
That means a significant chunk of health and safety risks go unnoticed because staff avoid or forget to report them. Let’s be honest: it’s hard to fix problems we don’t even know exist in the first place.
In the hectic bustle of a busy manufacturing environment, our teams have more important things to do than wrestle with outdated software or tedious paper forms. Too often, the incident reporting tools we rely upon seem to have been designed by folks who’ve never actually set foot on a shop floor. Manual reporting steps, overly complicated interfaces, and slow loading times turn simple safety actions into long-winded chores.
I remember finding half-filled incident reports scribbled hastily on notepads during site walkthroughs—clearly evidence of a workforce frustrated by poor design. And who can blame them? Time spent battling confusing paperwork or technology could be better invested into core tasks or actual safety improvements. When reporting safety risks takes longer than fixing them, it’s human nature to skip the hassle—regardless of best intentions.
Not only does this friction limit the quality and accuracy of our safety data, it can also undermine morale. Employees inevitably question why management can’t offer a simpler solution, potentially creating tensions and driving a wedge of resentment between frontline teams and management.
Through reflection and a fair share of trial-and-error, I’ve realised the importance of making the right solution incredibly easy to adopt in a real-world setting. What if, instead of forcing busy workers to stop everything to file laborious incident reports, we could automate some of the hassle away? I’m not talking fantasy, just practical automation tailored to everyday reality: the power of AI-enhanced EHS automation.
An AI-supported platform isn’t about replacing human judgement—it simply eliminates the repetition and time-wasting. Imagine a scenario where team members can verbally report incidents via smartphone or tablet on-site—after all, most of us are already almost surgically attached to our mobile devices! The software uses artificial intelligence to transcribe their words, categorise the incident, and prompt follow-up actions automatically. It’s also clever enough to identify and remind responsible staff members when follow-ups are missed.
Another practical tip: plugging AI-enabled safety reporting into existing digital checklists and dashboards that teams already use daily. The fewer foreign interfaces you introduce, the faster employee acceptance and compliance happen, dramatically reducing friction.
We’ve seen direct evidence of this at my own facility: incident reporting increased by a staggering 40% within three months after moving from clunky manual processes towards a simplified AI-driven approach embedded into tried-and-tested daily routines. Crucially, team morale improved significantly too. The way I see it, that’s two huge wins for the price of one.
When health and safety incidents go unreported—not from negligence, but from frustration—compliance inevitably suffers. But here’s the kicker: better reporting processes don’t just improve compliance with regulations and standards; they actively foster a healthy, engaged safety culture. Presenting frontline teams with smoother, intuitive ways to log and highlight safety concerns builds better habits.
We quickly realised that automating incident reporting wasn’t just ticking a regulatory box—it was building trust. Employees who see real-time action in response to their quickly-reported incidents feel their effort matters. In return, they report hazards proactively rather than reactively. Rather than begrudgingly filling forms (or skipping them altogether), they now actively look for ways to stay ahead of issues.
I won’t pretend we’ve reached incident-reporting Utopia. I still believe strongly in the human touch to interpreting health and safety data. AI still isn’t going to walk around on my shop floor and feel that subtle vibration or smell that particular odd odour. AI-supported EHS automation cannot—and shouldn’t—replace thoughtful human decisions.
What it absolutely can (and does) do, though, is make our jobs easier, bring unseen risks into the daylight faster, and hugely improve both regulatory compliance and team morale.
So next time you see a blank accident book page, half-filled-in forms gathering dust—or the telltale sign of your employees’ frustration at manual reporting tasks—perhaps pause for thought. Investing in practical, seamless AI-supported incident reporting tools that fit naturally into existing workflows may prove not a radical change, but a simple decision whose time has definitely come.
Have you ever caught yourself spending hours trawling through handwritten notes, blurry photos, and scattered forms after a workplace incident? Look, I’ll be honest here—I’ve been there myself. There was a time when I’d battle a growing pile of safety incident reports that felt like an eternal mountain of chaos. I thought there was no better way—because that’s just how we’d always done it. But here’s a tough pill to swallow: the old ways might just be the thing slowing you down.
Hear me out—I know paperwork feels reassuringly familiar, but what if the old “tried and tested” way is actually adding risk, cost, and stress to your profession? What if the piles of papers and manual filing systems are actually what’s holding your team’s performance back? Shifting perspective isn’t easy—but we’ve got to ask ourselves if our current health and safety processes serve us or trap us in an endless loop of inefficiency.
Here’s something from my experience: manual safety reporting processes are almost always reliable—for being a headache. Padding through paper forms, chasing team members for details weeks after the incident, and deciphering scribbled notes has, in hindsight, always been counterproductive at best, and potentially dangerous at worst. Yet, despite these obvious pitfalls, it’s what most of us started our careers doing, and it’s easy to fall back into old habits under pressure.
One costly danger I’ve seen repeatedly is incomplete or forgotten details. How many times have you struggled to get accurate witness testimony days after an event occurred? Or realised incident photos turned out too blurry to use, yet there was no way to retrieve that information again? Manual systems simply lack structure and consistency, and missing information doesn’t just cost paperwork—it risks safety decisions altogether.
Plus, let’s call this out for what it is: paper-based reporting drains precious hours from your schedule. Your skill set is too valuable to be burned on sifting through outdated, unclear forms and juggling conflicting details. And the kicker? This inefficiency directly impacts workplace safety because it restricts your capacity for proactive hazard prevention and health and safety strategy. Every unnecessary minute spent on filling, chasing, or storing papers is ultimately time lost managing real, actionable safety improvement.
Years ago, I remember vividly an incident where I discovered our traditional reporting system had become so convoluted that safety managers were deliberately choosing “shortcuts” through the process just to cope. Details got missed, near-misses weren’t properly logged, and staff became frustrated because the system genuinely got in their way. It was then I knew we had to find another way—one that made reporting incidents quicker, clearer, and more user-friendly.
That’s when I discovered digital safety systems. Imagine reporting an incident by simply snapping a photo using a tablet or smartphone and attaching a few automated details. No interminable form-filling session. No relying on fading memories days later. Just an instant, complete record of what exactly happened, when, and where, automatically synced to a centralised dashboard accessible at the touch of a button.
Safety report automation isn’t about replacing human insight. It’s not about fancy technology for the sake of it, either. It’s simply about providing clarity and ensuring crucial details aren’t overlooked. Yes, there’s initial scepticism, but consider this: would we accept outdated machinery in manufacturing knowing full well it would cost efficiency, quality, and overall competitiveness? Then why accept outdated machinery for incident reporting and management?
Since we moved towards health and safety automation, I’ve experienced a remarkable transformation on the shop floor and in our health and safety culture. It’s measurable, impactful, practical change. With automation in place, incident reports that used to soak up hours of staff time can now be submitted in less than two minutes. Details are instantly captured and integrated into our safety dashboard, allowing me to identify trends, understand risks better, and—most importantly—prevent further injuries altogether.
I couldn’t believe how much I actually dreaded paperwork until it was no longer a major part of my job. Automation didn’t just give me more hours in the day. It gave me insight, clarity, and—this might sound dramatic but trust me it’s true—a renewed sense of purpose. When you’re less burdened by admin, you’re free to invest more energy in prevention, strategy development, training, coaching your team proactively, and championing safety at every level.
Perhaps the biggest relief was our managers and staff no longer felt buried under frustrating processes. Safety became simpler, more inviting, and easier to prioritise. Automated incident handling has significantly reduced stress, and rather than chasing our tails reacting to incidents, we’re able to spend time preventing incidents altogether. Ultimately, isn’t that the real point of safety reporting—to drive prevention and keep employees safe?
If you’re still buried beneath sea-level in incident reports, snap out of it. Safety process automation isn’t about technology replacing people but technology empowering you to do what you’re best at: managing and promoting health and safety with clarity, ease, and total confidence. Embrace digital, simplify your workflow, and give yourself the space to invest more in what matters: building a workplace culture that prioritises genuine safety.
When I first took on health and safety responsibilities at our plant, audits terrified me; frankly, they still make even the best of us slightly nervous. Picture the scene: another busy collection day looming, and I’m knee-deep in boxes of illegible paperwork and past-month logbooks. The next morning—the dreaded audit visit. Despite my best efforts to maintain spotless records, audits always seem to coincide with the busiest days. It’s like the safety inspector had a sixth sense for maximum inconvenience.
I can still vividly remember sitting at my desk, staring at a coffee-stained accident form, trying desperately to decipher whether that was “tripped over hose” or “trapped by nose.” Time ticked away, tension built, and I found myself scrambling through endless filing cabinets, desperately hunting for a single piece of evidence. Even as a seasoned professional, I found myself repeatedly thinking: There must be a better way.
The issue wasn’t incompetence or bad luck, although at stressful times it certainly felt that way. The challenge was systemic. Managing health and safety compliance entirely by hand or with clunky outdated software inevitably leads to chaos. You’ve probably been there yourself—trying to persuade busy team members to accurately write reports in physical incident logbooks or updating spreadsheets manually at the end of a long shift.
Manual systems create friction at every turn, but even outdated software can be just as troublesome. Slow, poorly designed tools turn what should be quick, simple tasks into multi-step marathons. I’ve needed to ferry paperwork back and forth from my office to production floors simply because our old incident tracking system wasn’t accessible on the shop floor computer. Data duplication errors inevitably crept in, impossible to avoid no matter how meticulously everyone worked. Quite frankly, putting up with outdated reporting methods felt like sitting on a conveyor belt, hopelessly watching valuable working hours roll away from me, never to return.
I realised I couldn’t afford to ignore the creeping inefficiencies of our safety processes anymore. After considering our options—and trust me, I hesitated at first—we implemented digital safety systems that automated our manual and overly complicated tasks. Initially, transitioning to new software made me slightly nervous—I’m no tech wizard!—but thankfully the intuitive design made onboarding our team that much easier.
One of the strongest areas of transformation for us was incident reporting. Previously, whenever an accident happened, recording the event relied on hurriedly scribbled notes on clipboards or half-hearted jabs at outdated computers. Compare this to our current setup—a simple, user-friendly interface accessible directly from a mobile tablet, instantly available to everyone at the point of use.
Accident details are now entered directly as they happen, with automatic timestamps and location logging. Importantly, digital entries can capture accurate images, instant notifications can be sent to relevant team members, and everything is backed up securely in the cloud. Rather than spending valuable hours chasing down incomplete or incorrect incident forms, our team members now complete straightforward onboarding and reporting, and get straight back to business. It’s not magic—though it does feel a bit like it—but simply using the right safety compliance software can transform incident reporting and compliance tracking by leaps and bounds.
The change in our daily health and safety management has been profound. To put it bluntly, adopting digital safety systems wasn’t an expense; it was a necessary investment in sanity.
First, there’s the significant time saved. Previously, our weekly compliance housekeeping — reviewing handwritten reports and updating spreadsheet trackers—used to cost me several hours every Friday afternoon. Now, automated safety compliance software does most of the heavy lifting for me, enabling me to focus on training, prevention initiatives, and maybe even catching an occasional tea break.
Mistakes that once plagued our data entry—illegible forms, incorrect data duplicates, or misplaced files—have dramatically reduced. Digital tools help us maintain consistency across reports, ensuring that I’m confident in the accuracy and quality of our compliance records. This transparency and traceability also means colleagues naturally take reporting and safety record keeping more seriously, knowing their actions and data entries are captured instantly and transparently.
Finally, I’ve noticed my stress levels have plummeted. With digital backups, instant report access, and real-time data transparency, audits no longer fill me with dread. I’m audit-ready not just this week or this month, but throughout the entire year with minimal effort.
If you’d told me earlier in my career that achieving continuous audit readiness would someday seem effortless, I probably would’ve laughed bitterly over my pile of paperwork. Yet here we are. It’s not lazy—it’s simply smarter. And smarter is exactly how health and safety should operate.
Here to ensure future incidents are prevented by delivering robust compliance tracking systems.